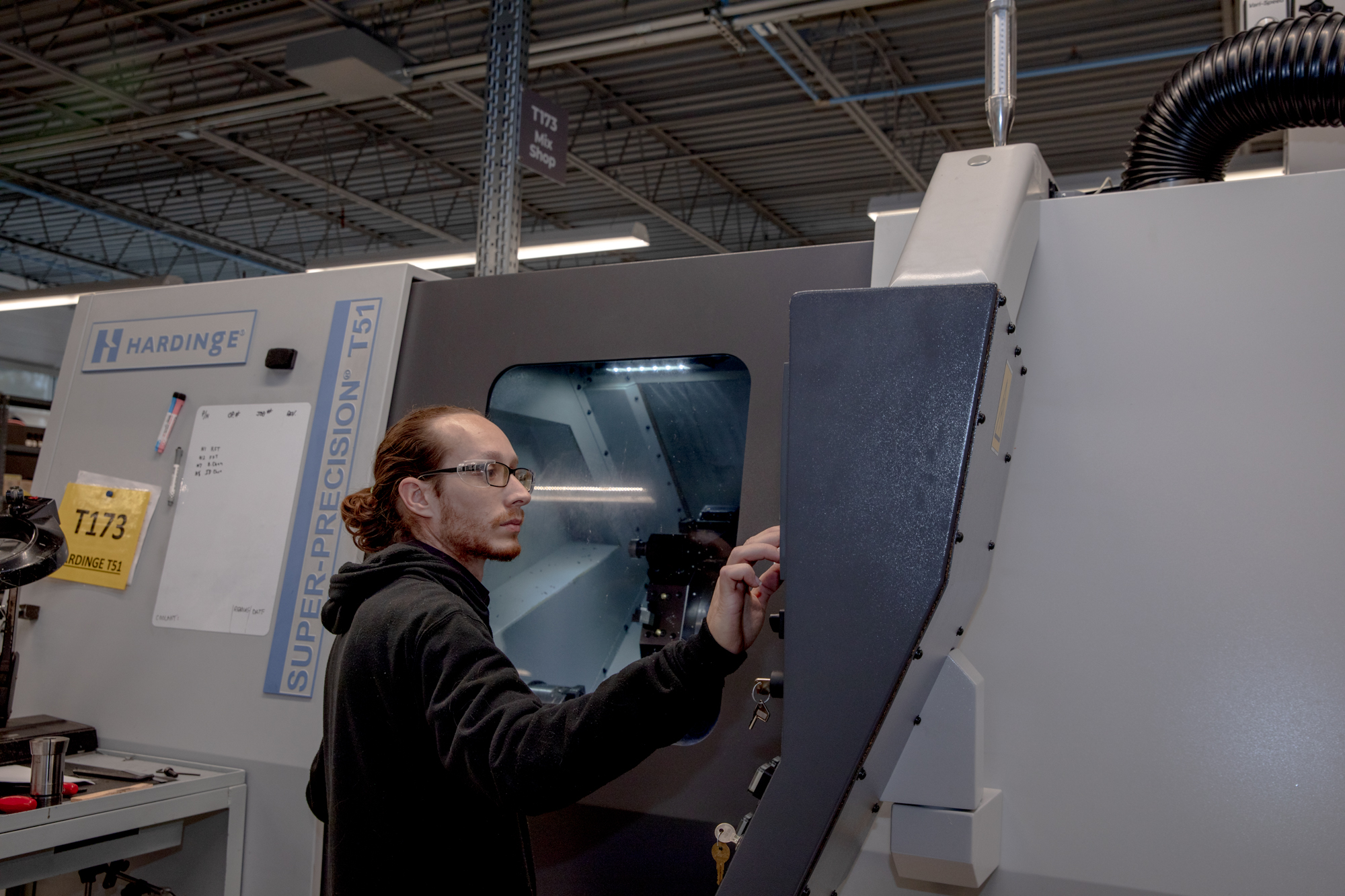
President-elect Donald Trump has promised to enact far more expansive tariffs than those he imposed during his first term, and the impact could be widespread — not only for Connecticut consumers but also for many locally-based businesses.
Trump has extolled tariffs, both as a way to raise revenue and as a strategy for boosting domestic industries by making foreign goods more expensive. During his first term, tariffs were applied to steel, aluminum, solar panels and many other Chinese goods. The Biden administration retained many of Trump’s tariffs, raised some and added a 100% levy on Chinese electric vehicles — all in an effort to protect the U.S. semiconductor, green energy and other industries.
Trump’s plan for tariffs this time around is far more broad.
During this year’s presidential campaign, Trump repeatedly promised 10% to 20% tariffs on all imports with the exception of goods from China that would see tariffs of 60% or more. The day before Election Day, Trump also suggested tariffs of 25% up to 200% on goods from Mexico as punishment for what he characterized as an “onslaught of criminals and drugs coming into our country.” (China and Mexico currently top the list of exporters to the U.S.)
Each year, trillions of dollars-worth of consumer electronics, clothing, toys, furniture, appliances and food pass through U.S. ports of entry alongside vast volumes of production inputs — from raw materials to component parts, machinery and equipment — that U.S. companies use in their domestic operations.
When tariffs are applied to intermediate and capital goods, as was the case during Trump’s first administration, “That directly increases the cost of doing business for these businesses that rely on imported components or machinery and equipment in their industrial process,” Erica York, an economist with the nonprofit Tax Foundation, said.
Tariffs are charged to the U.S. importer, whether that’s a retail business, manufacturer or otherwise. For consumer goods, the fees are commonly then tacked onto the retail sale price of each item. For manufacturing inputs — like materials, parts and equipment — the fees drive up production costs in the short-term, which can lead to price increases, reduced output, lower profits, or all of the above.
“That creates a competitive disadvantage for companies operating in the United States compared to companies operating in other countries that don’t face that same import tax,” York said.
Jay Timmons, president of the National Association of Manufacturers, said in a recent appearance on CNBC that the impact of any new tariffs will depend on how targeted they are and how they’re implemented.
“If they’re broad based, they could increase the cost of doing business here in the United States, which would lead to more inflation and would not be good for the American consumer,” he said.
Imports vs. exports
Economists also expect U.S. tariffs on imports to have negative effects on U.S. exports. Other countries are likely to impose retaliatory tariffs, making U.S. goods more expensive in foreign markets.
“Depending what foreign countries decide to target, that has another negative effect on U.S. businesses, because it reduces foreign demand for the products that they’re making,” York said. “That can be just another hit to income and another layer of uncertainty.”
Additionally, higher prices on imports to the U.S. could drive down demand for foreign goods; with U.S. buyers exchanging fewer dollars for foreign currency needed to buy foreign goods, the value of the dollar goes up, making U.S. goods more expensive to foreign buyers, York said.
“We sometimes say that a tax on imports is a tax on exports, and the connection between the two is the value of the currency,” York said.
For Connecticut’s many export-oriented businesses, the potential loss of demand from foreign customers is raising alarms, said Chris DiPentima, president of the Connecticut Business and Industry Association.
“The ability to ship end-products to customers outside of the U.S., that has to be a very smooth and efficient process. Otherwise the wheels of commerce will come to a halt and so will our economy,” DiPentima said.
CT companies mum for now
Most Connecticut companies aren’t willing to comment publicly on Trump’s proposed tariffs.
A spokesman for Norwalk-based Xerox declined an interview request. Representatives for other publicly-traded companies based in the state — including United Rentals, Terex, Amphenol, Silgan and Pitney Bowes — didn’t respond to requests for an interview.
Defense manufacturers with major operations in the state struck a similar note. Pratt & Whitney parent company RTX and Electric Boat parent General Dynamics both declined to comment. Several specialized defense supply chain manufacturers also declined interview requests.
In an emailed statement, a spokesperson for Lockheed Martin, parent company of Sikorsky, wrote: “It would be premature to speculate on any policy proposals at this time. We look forward to working with the Trump-Vance administration and the new Congress to support and strengthen our national defense.”
But the issue is clearly on the minds of many business leaders.
For New Britain toolmaker Stanley Black & Decker, tariffs could throw a wrench in many aspects of their business, from retail sales to supply chain and manufacturing operations. During a conference call discussing the company’s third quarter earnings last month, CEO Donald Allan said under any “new tariff regime,” the company would expect to raise prices. “We will work through getting those into the market in a reasonable time frame,” he said.
Allan went on to say that the company also planned to mitigate increased production costs “by moving production and aspects of the supply chain to different parts of the world.” That could include shifting operations from China to Mexico or other parts of Asia — though it’s unlikely any production would relocate to the U.S., he said.
“So we have a fairly robust plan. What we don’t know is which scenario is going to play out and exactly how that would be,” Allan said. (A spokeswoman for Stanley Black & Decker didn’t respond to emails seeking further comment.)
Shelton-based Hubbell Inc., which makes electrical products, also recently addressed its plans for the possibility of new tariffs with Wall Street analysts.
In the company’s most recent third quarter earnings call, CEO Gerben Bakker said Hubbell made changes to its supply chain in the last few years that “reduced our exposure” to higher costs associated with tariffs. Bakker said he’s “confident” they’ll have a smaller impact on the business as a result. (A spokesman for Hubbell declined to comment further.)
Working with Trump
For most Connecticut companies, it may be too early to tell how operations would be affected and how best to adjust. But they might be looking back at what happened during Trump’s previous term for clues.
York said the first Trump administration allowed companies to apply for exemptions to certain tariffs, granting them to select applicants. Researchers later found those exemptions more often went to companies that made contributions to Republican politicians.
York said that could happen again. “This actually opens the door for a bunch of shady political bargaining,” she said. “Not good outcomes.”
There’s also some question about what the Trump administration aims to achieve by imposing tariffs on such a wide range of imports. Tariffs can serve to raise government revenue, which could cover part of the cost of the incoming administration’s proposed tax cuts.
But tariffs are also used as a tool to encourage the development of domestic industries. If they succeed in that respect, imports decline and tariffs’ potential to raise revenue diminishes.
“Really, what a tariff does is kind of reallocate where business activity is happening,” York said.
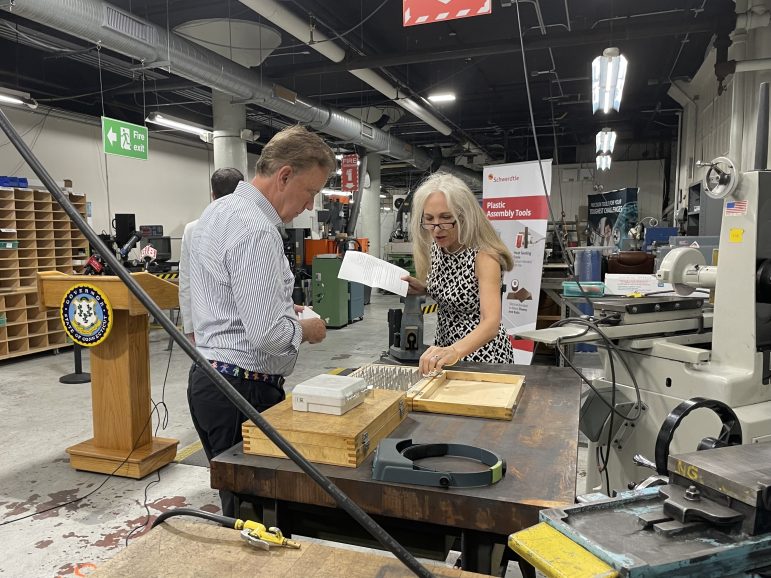
U.S. Rep. Rosa DeLauro, D-3rd District, said in an emailed statement that she supports “targeted tariffs” in areas like renewable energy and defense to “ensure that we are not yielding our technological edge to global adversaries like China.”
But she added that she’s concerned Trump’s proposal to raise tariffs on nearly all imports “would be devastating for American families and the middle class, who continue to struggle a rising cost of living, for American businesses across all sectors that rely on imported goods anywhere in their supply chains, and for American workers who are the source of our economic strength and competitiveness.”
DeLauro said she worked with the previous Trump administration on trade policy and she expects to continue that work during the coming term.
Pedro Soto, owner and chief executive of Hygrade Precision Technologies, a precision metal grinding business in Plainville, said tariffs won’t affect his company in the short-term because it doesn’t import materials or components — it sells its finishing services to parts manufacturers.
In the medium- to long-term, if tariffs do drive a resurgence in U.S. manufacturing, businesses like Hygrade could benefit, Soto said. “If parts were being made in China or Mexico or India and now they’re coming here, they may need the special processes that we do, that were being done over there,” he said.
“That may be where the supply chains have to start to grow,” he said. “And there may be some opportunity there to, A., help, and B., make some money on that.”